Standardizing Single-Use
By Hélène Pora, Vice President Technical Communication & Regulatory Strategy, Pall Biotech
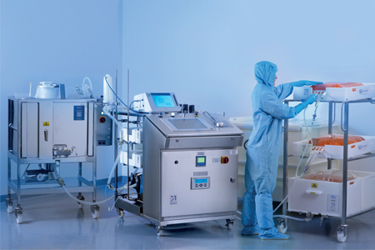
Single-use processing equipment now dominates pre-commercial biomanufacturing and is becoming an increasingly popular option at the commercial scale. The benefits are clear: pre-sterilized single-use systems can reduce setup and changeover times, while eliminating the costs associated with cleaning and its validation and they are associated with a high degree of flexibility to accelerate time to market. As demand for single use has grown, so too has the number of single-use systems on the market – with a wide variety of components, consumables and sensors. But the proliferation of choice has also led to a need for some degree of standardization. This question is more difficult than it first appears, as there many interpretations of what standardization really means in the world of single-use technology.
Single-use systems contain tubes, bags and filters, and different vendors will use different types of materials of construction for their components. The lack of standardization means that end-users may have to go through complex validation testing protocols for the combination of components they use. To complicate matters further, biopharmaceutical manufacturers often use different single-use systems and components, in different combinations, at different sites – or even within the same site at separate buildings. And that can make extractables and leachables studies complex and expensive.
A degree of standardization would reduce the risk inherent in the process, streamline the supply chain and reduce development times, thereby reducing costs and improving product quality. Of course, standardization does not mean everyone in the industry uses the same pieces of equipment, with the same designs – flexibility and using the right equipment for the process is important. A lot can already be achieved by using similar practices and standardizing the components used. Systems have a tendency to drift apart over time, and it’s important not to let entropy take over – new single-use systems or stock keeping units (SKU) shouldn’t be put in place unless there is a clear need to do so. A central benefit of this approach is that it makes validation much easier. If the components have been used before within a company or a manufacturing site, the validation documentation should already exist or can at least be adapted – much easier than starting from scratch. Using the same SKUs for multiple applications can also reduce inventory size, which in turn can reduce the warehouse space required – a big bonus given the space requirements of single-use systems. All of this can lead to reduced costs and lead times.
Get unlimited access to:
Enter your credentials below to log in. Not yet a member of Drug Discovery Online? Subscribe today.