Berkeley Lab's Prep Track Offers High-Throughput Microplate Handling
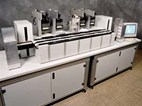
Recently, the needs for higher throughput have pushed the evolution of pipetting robots to 96-channel systems. Both fixed- and removable-tip systems are being manufactured by Robbins, Sagian, Tomtec, Matrix Technologies, SAIC, and others. High-throughput "sequencing centers" have evolved that standardize and configure liquid handling protocols to take advantage of these 96-channel liquid-handling systems. These liquid handling systems are typically used for plate filling, PCR setups, and sequencing reaction setups.
To bring the power of assembly line-style automation to high-throughput biotechnology operations, Lawrence Berkeley Lab has developed Prep Track, a modular conveyor for sequentially processing biochemical samples in standard microtiter plate formats.
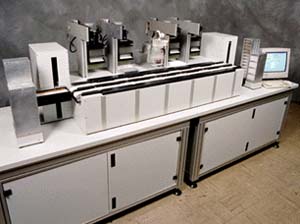
PrepTrack uses two parallel belts to move biological samples in standard microtiter plates through modular workstations in a manner similar to assembly-line factory automation.
In Prep Track, two continuously moving belts pass over the modules, each of which is optimized to perform a single task with maximum parallelism. When instructed, the module intercepts the plate, raises it up off the belt, performs its function, and redeposits it to the belt where it passes down the line. With two belts, replicates can be made from master source plates. Similarly, complementary reactions in multiple target places may be set up.
Source sample and blank plates are fed in from cassettes mounted on carousels at one end, and re-stacked upon completion at the other end. Modules conform to a standard geometry and communications interface, so the system may be flexibly reconfigured for changing protocols.
Modular Design for Greater Flexibility
Prep Track's current design supports eight standard modules, which are configurable in any order. Standardization of the mechanical, electrical, and communication components of each module allows for new modules to be easily designed and manufactured. The current standard module footprint is 250 mm wide and 600 mm deep, rising 250 mm above the conveyor belt deck.
To date, Berkeley has designed modules for full plate sample transfer (96 independent pipets in parallel) and for full plate dispensing (96 needles in common). Other modules handle less common microtiter plate-based processes and assays. When working in PCR cycle sequencing reactions, plates exit the system at a throughput of 250 plates per hour.
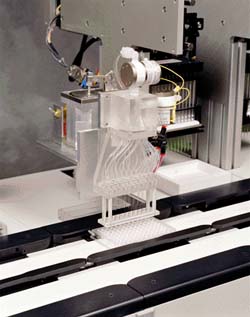
The high-volume dispenser station is capable of dispensing liquids in volumes from as low as 5 microliters to several milliliters. It operates by releasing liquid flow from pressurized (10 psi) liquid reservoirs for defined time periods. This module has 24 dispenser channels. The current protocol calls for dispensing 189 microliters of water to a standard microtiter plate. The dispense time is approximately 500 milliseconds for 24 channels.
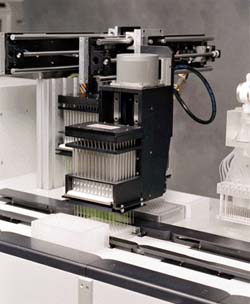
The 96-channel pipettor modules are modified Robbins 96-channel pipettors. Each of these modules is configured with ninety-six 250 microliter fixed tip syringes. These modules are used to transfer liquids from one plate to another on each of the conveyor belts. Each module has cleaning reservoirs for washing the syringes between plate transfers.
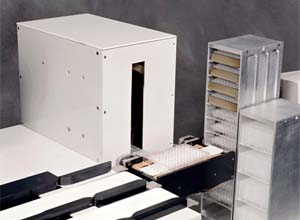
There is a plate fetching module at the input and the output of the system. This consists of an elevator (Z-axis motion) and a fetching mechanism capable of placing and removing microtiter plates to and from the conveyor belts, and transferring them to and from the input and output cassettes in any combination.
The microtiter plates are stored in input and output cassettes, which accommodate a wide variety of microtiter plates including standard and deep well formats. The first "Prep-Track" has two fixed cassettes positioned at each end of the system: the second system built incorporates carousels of cassettes at each end.
Liquid handling modules have their own separate conveyor belt intercept station which stop the plate, lift it slightly off of the conveyor belt, and position it accurately for processing.
Each module is independently controlled by programmable logic controllers. The overall system is controlled by a PC running a Visual Basic master control program, which controls the order in which plates are processed through the system. The actions of each lift station and dispenser/pipettor are locally controlled by programs resident in each module's PLC. The Visual Basic program moves plates through the system based on the predefined protocol and the status reports of each module as monitored by the PLC's.
For more information: Martin Pollard, Project Director, Prep Track, EGME 1, MS PSF, Lawrence Berkeley Laboratory, 1 Cyclotron Rd., Berkeley, CA 94720. Tel: 925-296-5632. Fax: 925-296-5666.
By Angelo DePalma